In 2018, a devastating explosion tore through the Didion Milling Inc. corn milling facility in Cambria, Wisconsin, USA. Didion Milling Inc. is an agricultural processing and co-located bioscience facility specialising in dry corn mill, industrial alcohol and ethanol products. The explosion erupted after combustible corn dust ignited due to poor accumulation control, destroying large sections of the plant. Five workers lost their lives, 14 others were injured, and the facility suffered catastrophic damage. Investigators uncovered serious and repeated maintenance failures. The company had failed to install venting or suppression systems on a dust collector, neglected effective dust control practices, and falsified equipment records. These issues persisted despite prior Occupation Safety Health Administration (OSHA) citations for similar hazards. This tragic case highlights the high stakes of fire and explosions hazards in the food manufacturing sector, and the urgent need for effective risk and barrier management strategies.
This was not an isolated case. Fires and explosions continue to pose a serious and recurring threat in the food and beverage manufacturing industry. Factors such as combustible dust, high-temperature equipment, flammable materials and continuous production cycles all contribute to an elevated risk profile.
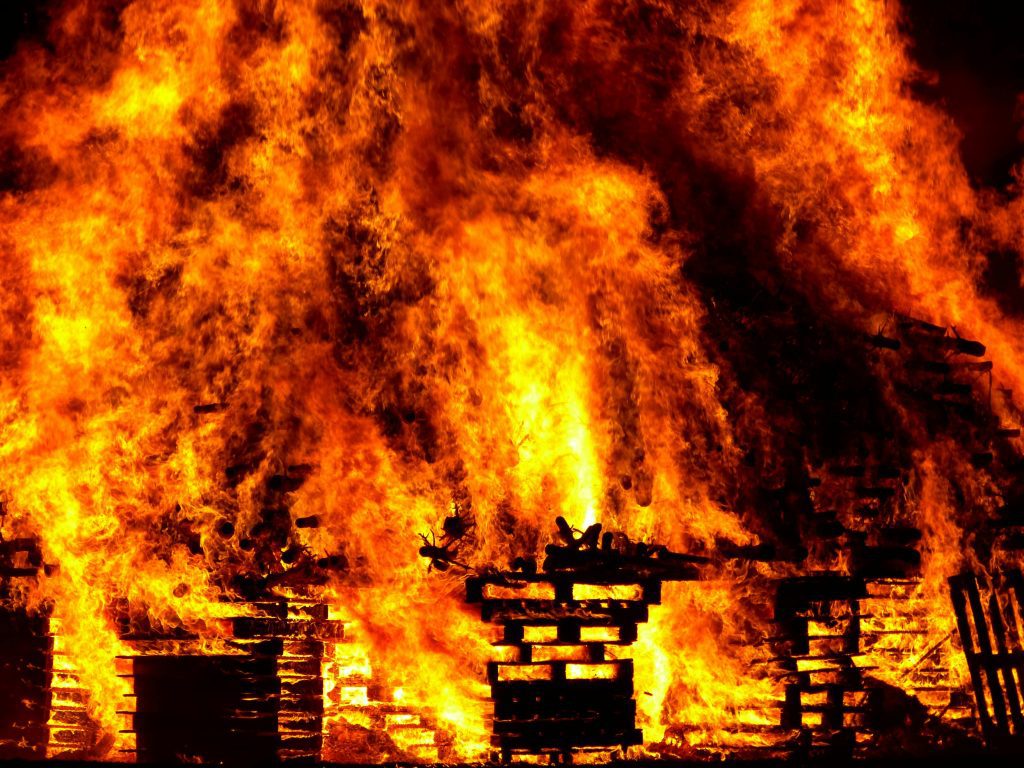
Pallets on fire in manufacturing industry
Understanding the Risk Landscape for Fire and Explosion using Bowtie Model
The causes of fire and explosions in manufacturing are diverse. The causes and threats can be mapped out using tools such as Presight OpenRisk which uses the bowtie model referenced above.
Causes include:
- Combustible materials
- Electrical faults
- Hot work activities
- Equipment failures
- Dust explosions
Each cause is associated with a set of preventive controls, including employee training, proper storage, routine inspections, and hazard area classification. A single weak or missing barrier can significantly increase the likelihood of a critical incident.
On the consequence side, fires and explosions can result in:
- Injury or loss of life
- Environmental impact
- Property damage
- Regulatory penalties
- Financial loss
Barrier Management in Practice
Barrier management plays a critical role in addressing these risks. A bowtie diagram visualises the progression from hazard to consequence, identifying which preventive and mitigating measures are in place and making visible any missing, outdated, or insufficient barriers that may compromise risk control.
Preventing Incidents: Heating, Cooling, and Containment
In food and beverage manufacturing, controlling temperature and isolating flammable materials is essential. Bowtie analysis helps identify necessary controls, such as inertia systems, grounding and bonding measures, or secure storage solutions, that must be established to prevent ignition.
- Heating systems require thermal cutoffs, regular inspection and engineered safeguards.
- Cooling systems demand routine maintenance to prevent overheating or refrigerant leaks.
- Containment strategies, such as segregation of combustible materials and implementation of leak detection, must be enforced consistently.
Managing Maintenance Risk with barrier-based thinking
Faulty maintenance frequently contributes to incidents. Barrier-based thinking makes it possible to:
- Map out which protections are in place against poor repairs or overlooked inspections.
- Increase visibility for tasks such as equipment calibration, inspection schedules, and employee competency management.
Proactive maintenance, guided by bowtie methodology, significantly reduces the likelihood of unexpected failures.
The Role of Digital Bowtie Tools such as OpenRisk
Many teams rely on spreadsheets, memory, or fragmented documentation. Presight OpenRisk provides a web-based platform that supports structured bowtie analysis and centralised management of safety information.
- Create and update bowtie diagrams in a unified workspace
- Filter bowties by meta data, barrier type, such as human or technical for responsible personnel, and safety standards
Presight OpenRisk improves accessibility to risk information, facilitates systematic barrier management, and strengthens the integration of safety into daily operations.
Conclusion
Fire and explosions risk in manufacturing are not only technical challenges but also operational, reputational, and human concerns. Barrier management using bowtie analysis brings clarity, structure, and resilience to safety strategies.
Addressing these risks effectively requires foresight and consistent action. Barrier visibility and integrity must remain central to risk management efforts.
Begin building and managing bowtie diagrams that strengthen operational safety and compliance.
Explore and sign up for free for Presight OpenRisk now at: openrisk.presight.com
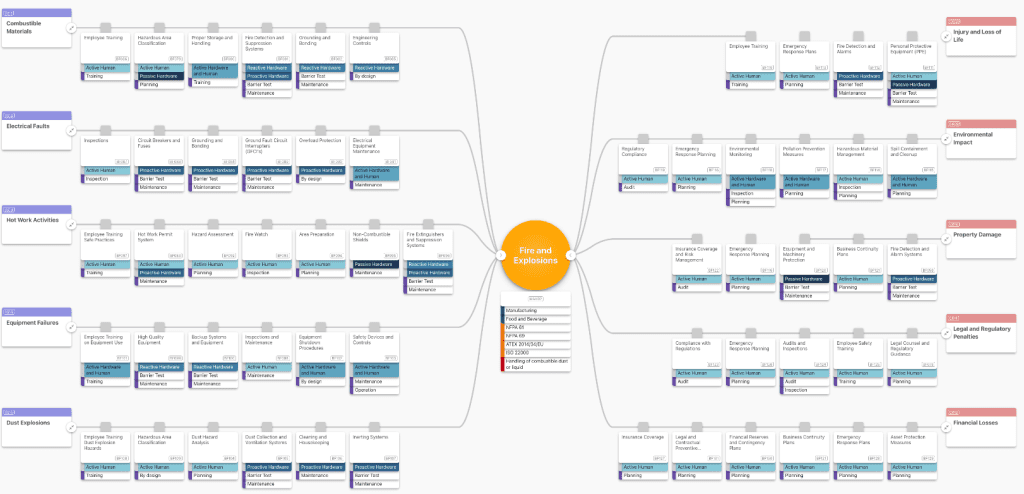