Loss of Containment (LoC) occurs when a hazardous substance escapes from the system designed to hold it. This may involve gases like ammonia, as well as liquids or solids leaking from tanks, pipelines, valves, or vessels. In many industries this is dangerous, but in the oil and gas sector, it can be catastrophic. A loss of containment incident can trigger explosions, fires, toxic exposures, and environmental pollution. The question “What is loss of containment?” often comes up in safety and risk discussions. The answer: companies fail to keep hazardous substances securely contained. And it remains one of the most serious operational risks. In high-risk environments, structured tools like Presight OpenRisk can support teams in mapping their risk picture and identifying vulnerabilities and evaluating preventive measures.
Causes, Consequences, and Real-World Examples
There is no single cause of LoC. The most common loss of containment causes include equipment failure, corrosion, poor maintenance, incorrect installation, and human factor causes. A corroded pipe, an overfilled tank, or a faulty pressure relief valve can all result in unintended release.
In some cases, operators detect a minor leak early and manage it before it escalates. But in others, the situation escalates. Well-known loss of containment incidents, such as the Bhopal gas tragedy, show how a single point of failure can lead to disaster. In Bhopal, a runaway chemical reaction combined with failed safety systems triggered a chain of devastating consequences.
Each loss of containment hazard is unique, but all require a proactive, structured response. When systems are complex, like offshore platforms or chemical plants, the margin for error becomes dangerously small.
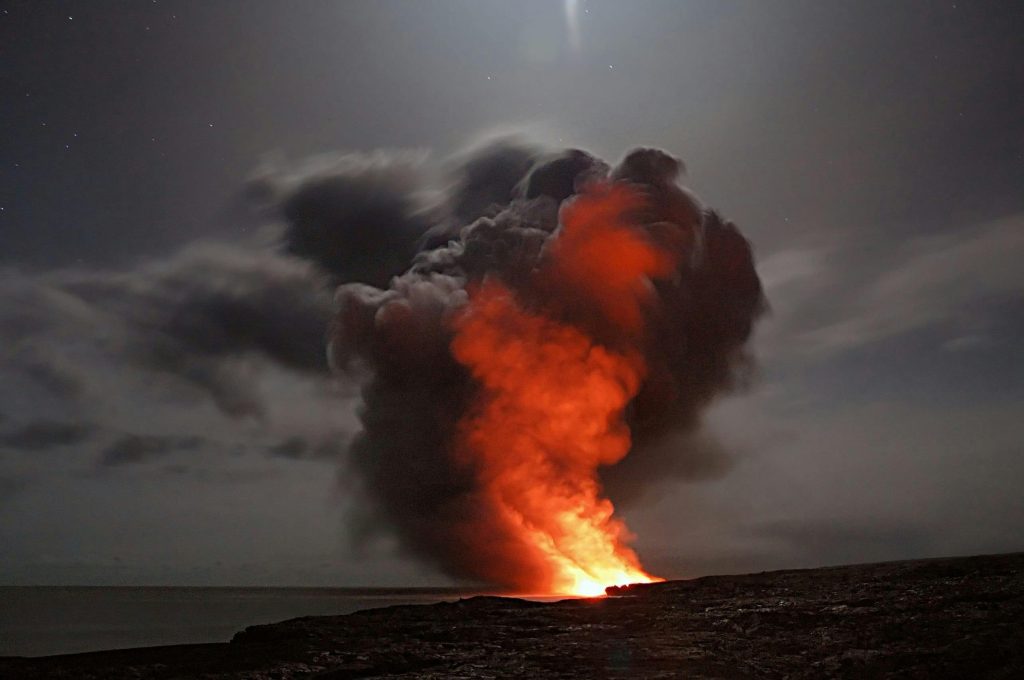
Managing the Risks of Loss of Containment hazards
Loss of containment means a substance escapes its intended boundaries. What matters is understanding why this happens and how to prevent it.
This means going beyond technical inspections. It requires thinking in systems, recognising early warning signs, and investing in organisational learning.
Bowtie diagrams help teams visualise how they can prevent LoC incidents and mitigate associated risks. A bowtie maps the path from potential causes to consequences and shows the preventive and mitigative barriers in place. It gives teams a shared understanding of risk and of where gaps might exist.
Digital Tools and Smart Barrier Management
Modern barrier management systems, such as Presight Barrier Management, take this a step further. Presight Barrier Management, not only identifies existing barriers, but also monitors their functionality. This close to real-time insight is critical.
For organisations looking for a simpler entry point, Presight OpenRisk offers a user-friendly way to apply the same barrier-based risk management principles. It simplifies bowtie modelling, enables quick hazard identification, and allows users to assign and track barrier responsibilities. All without the need for complex software or extensive training. This makes structured risk management accessible even to smaller teams.
Presight OpenRisk also supports bowtie diagram loss of containment mapping, helping users visualise risks and manage them effectively.
Loss of Containment can be managed using Safety tools
The oil and gas industry cannot afford to treat loss of containment as just another technical issue, meaning it cannot risk ignoring or underestimating it. It poses systemic threats to operations, safety, reputation, and regulatory compliance.
Managing it requires the right tools, the right mindset, and continuous attention.
With digital systems like Presight’s barrier management platform and accessible tools like OpenRisk, companies are better equipped than ever to prevent LoC events before they happen. Because once containment is lost, the consequences often come fast and without warning.
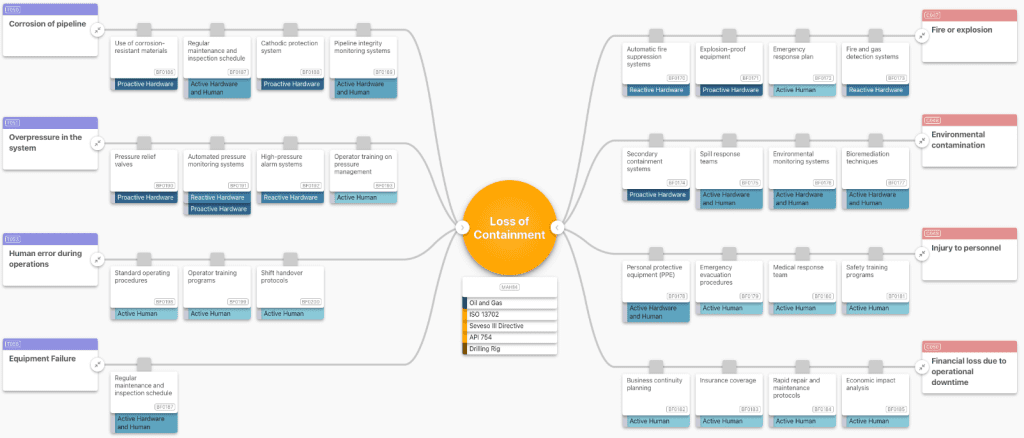