(This article was first published sep.3 2014 for IADC)
System turns risk analyses, safety cases and complex data into KPIs to ensure barriers function when needed
By Karl Erik Dahl, Presight Solutions
“Personnel shall be aware of which barriers are not functioning or have been impaired.” This is the sentence wherein the Petroleum Safety Authority (PSA) Norway has defined, in regulations, the challenge to companies operating on the Norwegian Continental Shelf (NCS) to reduce risk of major accidents.
The following is taken from PSA’s Management Regulation Section 5: Barriers shall be established that:
a) Reduce the probability of failures and hazard and accident situations developing; and
b) Limit possible harm and disadvantages.
Where more than one barrier is necessary, there shall be sufficient independence between barriers. The operator or the party responsible for operation of an offshore or onshore facility shall stipulate the strategies and principles that form the basis for design, use and maintenance of barriers so that the barriers’ function is safeguarded throughout the offshore or onshore facility’s life.
Personnel shall be aware of what barriers have been established and which function they are intended to fulfill, as well as what performance requirements have been defined in respect of the technical, operational or organizational elements necessary for the individual barrier to be effective. Personnel shall be aware of which barriers are not functioning or have been impaired. The responsible party shall implement the necessary measures to remedy or compensate for missing or impaired barriers.
PSA’s Management Regulation Section 10 states: The responsible party shall establish measurement parameters to monitor factors of significance to health, safety and the environment, including the degree of achievement. The operator or the party responsible for operation of an offshore or onshore facility shall establish indicators to monitor changes and trends in the major accident risk and environmental risk.
Learning from the past
The major accidents – Alexander L. Kielland (Norway, 1980), with the loss of 123 lives, and Piper Alpha (UK, 1988), with the loss of 167 lives – are important to mention. They fundamentally changed the industry’s understanding of risk, regulations and the approach to oil and gas activities in Norway and the UK, not least on the failure to understand risk and the factors that cause major accidents.
The referenced PSA regulation points on barrier and major accidents risk have not altered much over the past decade. Tragically, major accidents in the industry have continued to happen.
Deepwater Horizon (DwH) and Montara became wake-up calls to the authorities and to the industry as a whole. On the NCS, authorities, professional bodies and industry risk experts responded with analyses and recommended areas for improvement.
Following are extracts from the final 2014 PSA summary report on DwH:
Investigations of the DwH accident published so far have not identified new underlying causal mechanisms or causes. The DwH accident confirms that major accidents must be regarded as the result of a system error – in other words, a failure over time in a system of interconnected, to some extent mutually interdependent, players and processes.
Conducting a critical review of the information used to manage major accident risk is one of the measures relevant for the companies. This work could include an assessment of
• The relevance, reliability and modernity of the indicators used to follow up risk trends;
• Inappropriate use of indicators, incentives and reward systems;
• The need for better indicators and other information about the business which can be used to secure an early warning about a weakening in safety-critical barrier elements.
The solution to the challenge is not new regulations but enhancing its responsibility to continuously improve its safety performance to reduce risk and return value to society. This view underpins Norway’s regulatory approach to offshore HSE. It also means that a fundamental understanding of the factors that influence risk, including technical integrity and barrier status, is essential during operations.
Meeting the challenge and making sense of it
Under the PSA’s management regulations, the responsible company must identify the incidents it must guard against. These are known as defined situations of hazard and accident (DSHAs). Examples of DSHAs with potential for causing major accidents in the petroleum industry include leaks of flammable gas or liquids, well control incidents, fire/explosion in other areas, collisions and other structural damage to a facility.
A performance-based approach to regulations in Norway means that the PSA does not specify how companies should do this. The PSA only states in regulations what is expected from the industry operating on the NCS. This means that the industry has different approaches to solve the same objectives, and the list of DSHAs can vary slightly depending on the operation and the asset type.
The identification and listing of DSHAs and barrier or safety-critical elements in the companies’ risk assessment or performance standards is the starting point in the implementation of Presight Solutions’ KPI monitoring software.
Barriers and barrier effectiveness are elements in safety studies such as quality risk assessments, safety cases, safety integrity level studies, risk-based inspections, reliability-centered maintenance programs, HAZIDs and HAZOPs. These studies are used to establish barrier requirements and to assess the given safety or risk level with a given barrier effectiveness.
This graph illustrates PSA Norway’s guidance for barrier management in operations on the Norwegian Continental Shelf (NCS). The PSA has stated in regulations that companies operating on the NCS must ensure and maintain the required performance of barriers.
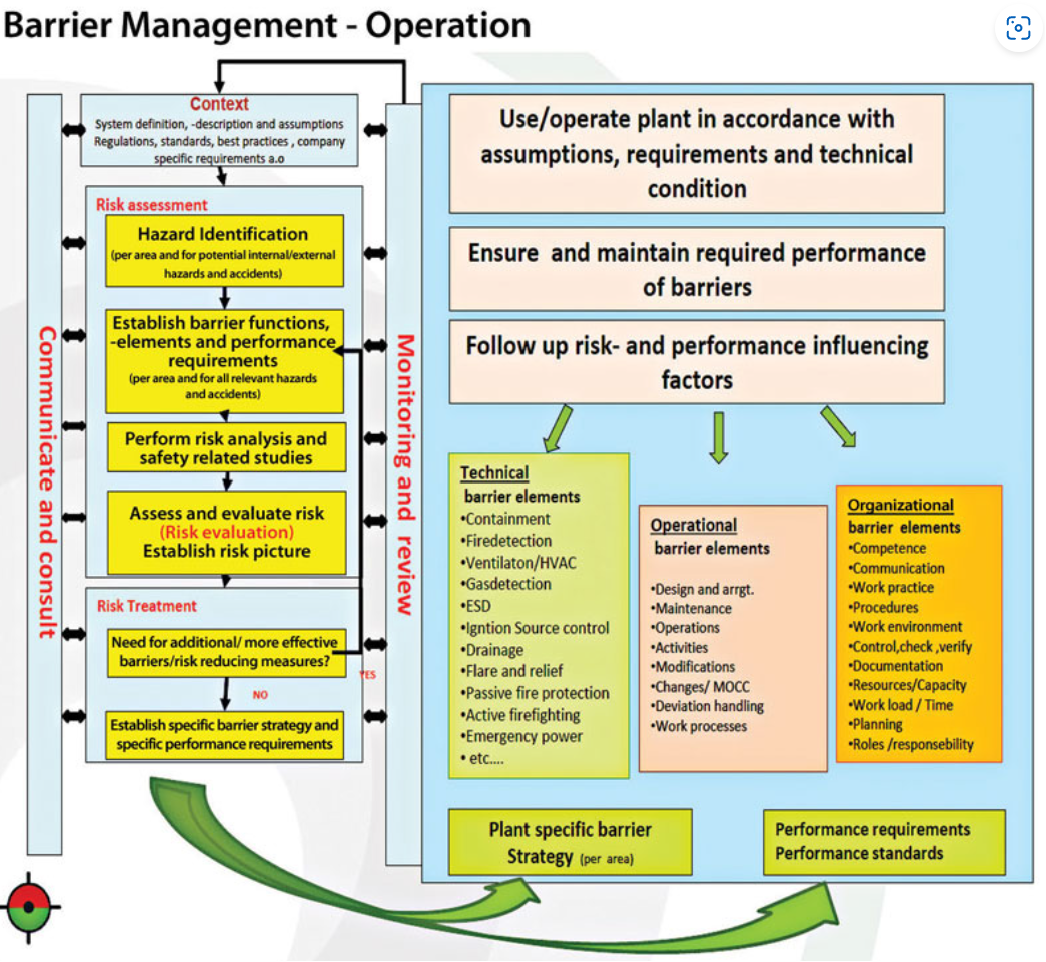
A common industry approach is to use bow-tie tools to describe, for example, the major accident scenarios, identify barriers as either preventive or mitigating, link barriers to specific hazards/consequences and include functions to identify barrier degradation mechanisms and measures to maintain barrier condition and performance. The Presight system’s aim is to provide companies with leading process safety and barrier performance indicators for crew and management in decision-making situations.
Presight Solutions CEO Petter Holst Johnsen explained, “Our role in implementing leading process safety KPI management has been to use the information available and relevant for assessing the status of barriers elements and then organize the information in Presight to display and communicate the status of barrier functions related to planning, operating and maintaining the rig.”
The main foundation for the implementation, he continued, is that the company has the required procedures and systems in place for barriers to meet the criteria set by the authorities, classifications society, standards institutes, equipment providers and internal company and asset-specific performance standards. After implementing the relevant barrier element indicators in the KPI system, the work turns to integrating and automating data collection from the company’s underlying source systems. These include maintenance, engineering and control, incident and non-conformity, HR/enterprise resource planning, procedures and documentation, training, inspections and drills.
An area for continuous improvement is the consistency and structure of the relevant data in the foundation systems. Certificates, courses, competencies, inspections, equipment and process, etc, should be organized in such a way that it is accessible for monitoring by the KPI management tool. Currently, system improvements are often identified and/or workarounds are required to reformat the data. The goal is to make information, such as frequency, revision, dates, complete or success criteria, and change of conditions, system-driven and automatic to remove the need for manual entry.
Performance of each element may then be monitored, and influencing factors can be found from condition and predictive maintenance data, POB/rotation and weather forecast.
Having a positive impact in operations
Leading process safety KPIs requires and forces information transparency across company operations, processes and systems. During the initial phase of implementing a KPI monitoring system, minor apprehension from employees can be observed. Individuals may be concerned that the drive for information transparency across the company will lead other departments in the organization to see “how far behind we are.” However, it should be remembered that compartmentalization of information and deficient communication were important underlying causes identified in reports from the DwH accident.
These concerns can be addressed through crew and section leader engagement in workshops, both in preparation for and during the implementation of the Presight system. The workshops focus on why a leading process safety KPI management system is needed and verifying the what and the how to include the right MTO (man, technology, organization) barrier element for monitoring.
It is worth noting that representatives from offshore and onshore teams participate together in the workshops. This helps to address differences of understanding and terminology for improvements to their management systems. It also helps to clarify what the information should be used for, by whom and when.
Applying a heuristic approach, after organizing and applying the relevant barrier element aggregation methods and risk weighting, the complex social-technical information is transformed into graphical interfaces in the monitoring system to provide visualization of barriers and performance functions for context- and user-focused decision support. This overall process of workforce engagement heightens risk awareness and understanding of responsibility, attributes of collective mindfulness.
From the leading process safety KPIs, users will drill down directly to the underlying data and system sources. Along with the use of signals, pies and graphs, this will allow the organization to prioritize actions. From a training and competence perspective, for example, leading process safety KPIs changes the focus from “how many have we not trained” to “who do we need to train now” to support offshore operations and meet performance standards.
One observation that has been made in implementation is that red signals are not necessarily bad, because now they know and can do something about it.
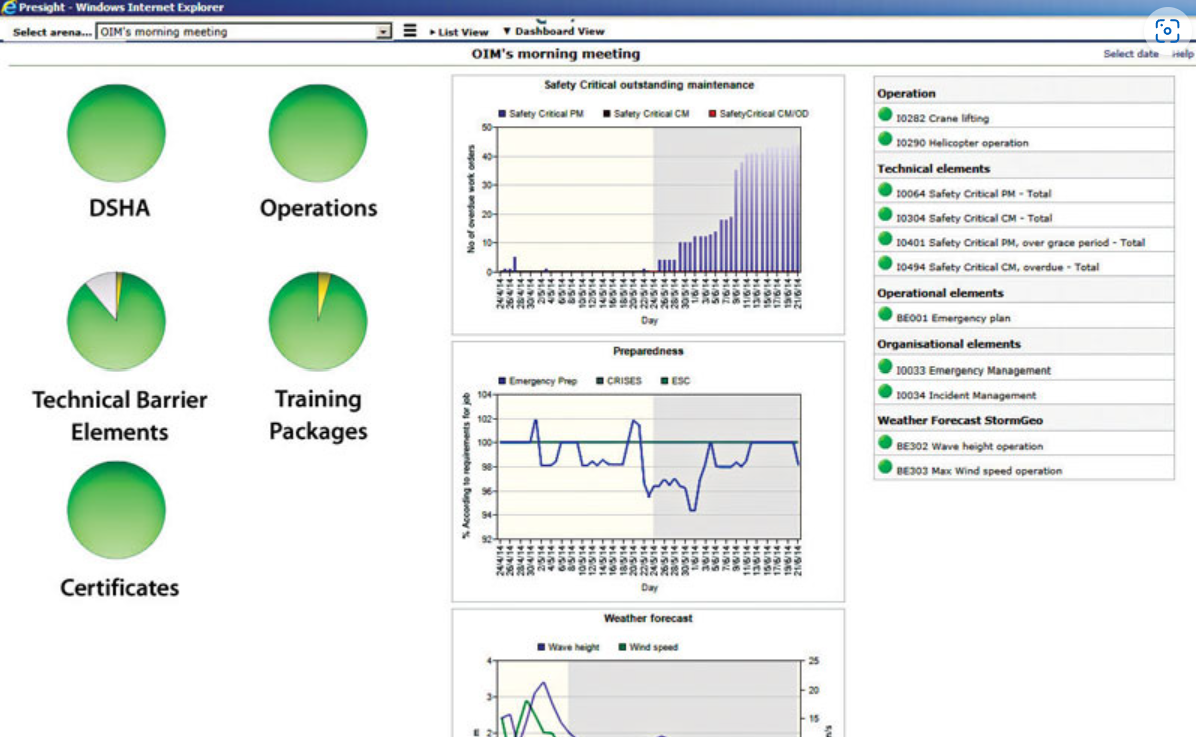
This example setup from the Presight system shows the monitoring of DSHA and barrier elements status organized for decision support in the OIM morning meeting. The graphs go forward for two additional weeks to direct attention to outstanding safety-critical maintenance and emergency preparedness.
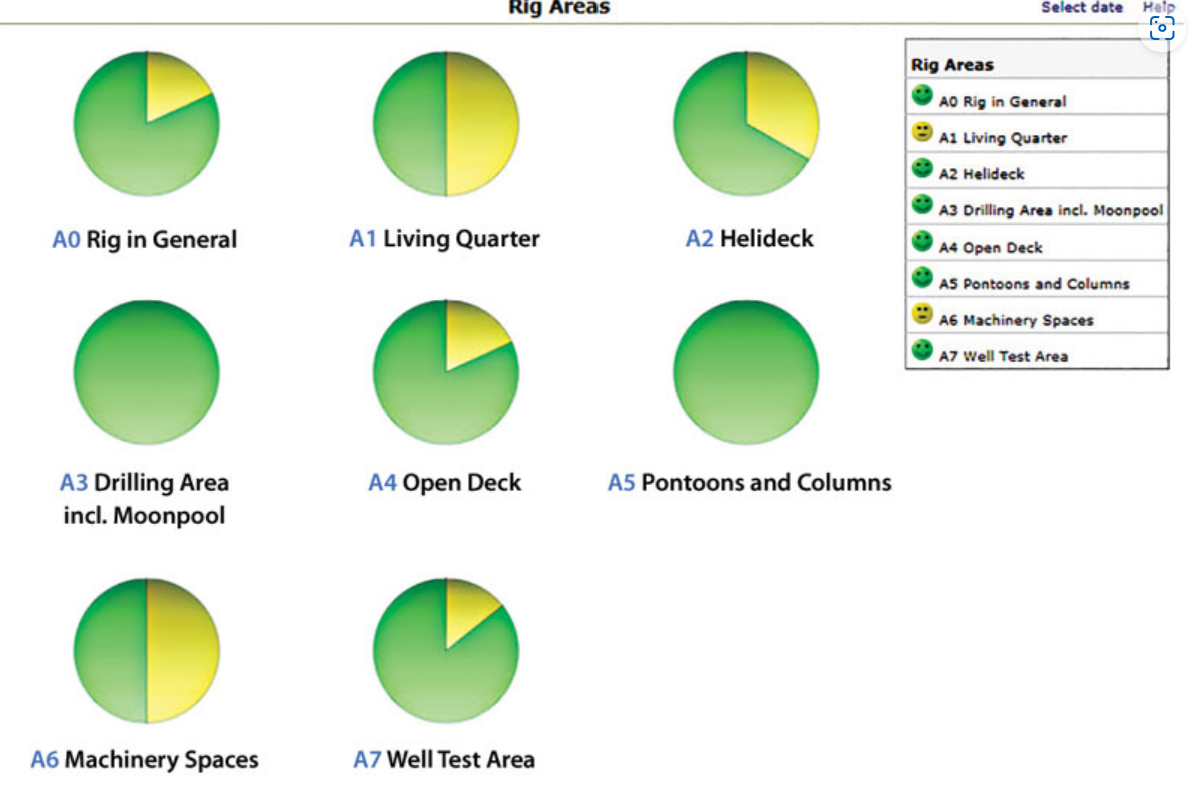
This example setup in the Presight system shows monitoring of DSHAs and barrier elements organized by rig area.
Industry dependent on society acceptance
Senior Presight Solutions Advisor Magne Ognedal, ex-Director General of the PSA, offers this perspective when discussing implementation of a leading process safety KPI management system: “The industry is totally dependent on two things. One is the access to new acreage, and the other is license to operate, or society acceptance. If you don’t manage these properly, the industry will be in trouble. It looks like the industry will more and more be required to prove that the management systems give the necessary oversight and control of major accident risk.”
An important part of this proof is the ability to demonstrate necessary competence, capacity, oversight, continuous improvement, processes, etc. Every company and person in the industry has a responsibility related to their role in the industry, Mr Ognedal said.
To illustrate the point about proof, the industry must be prepared now and in the future to properly answer questions like, how do you know that the barriers will be effective if they are needed? How do you know not that they worked half a year ago but know that they work today and will work tomorrow? An increase in risk due to unavailability of the barrier when needed is not acceptable.
The challenge is that these issues have to be managed, and the world is becoming more and more complex. The industry must, therefore, actively seek the information to then be able to see and understand the barrier elements to manage operations in a safe manner. Important to this point is that people need to understand what risk means, what the barrier elements are, why they are in place and, most importantly, that people can understand their own role as part of the barrier function.
After that, the industry needs to answer the big question: How do people, both on the rig and onshore, know that the barrier elements are in place, that they are functioning as they should and that they will work when they are needed to prevent another major accident occurring?
This challenge and improvement potential has been defined by the industry and the authorities. The Presight leading process safety KPI management system has been one step, taken by several companies on the NCS, as their way to support the industry’s license to operate.